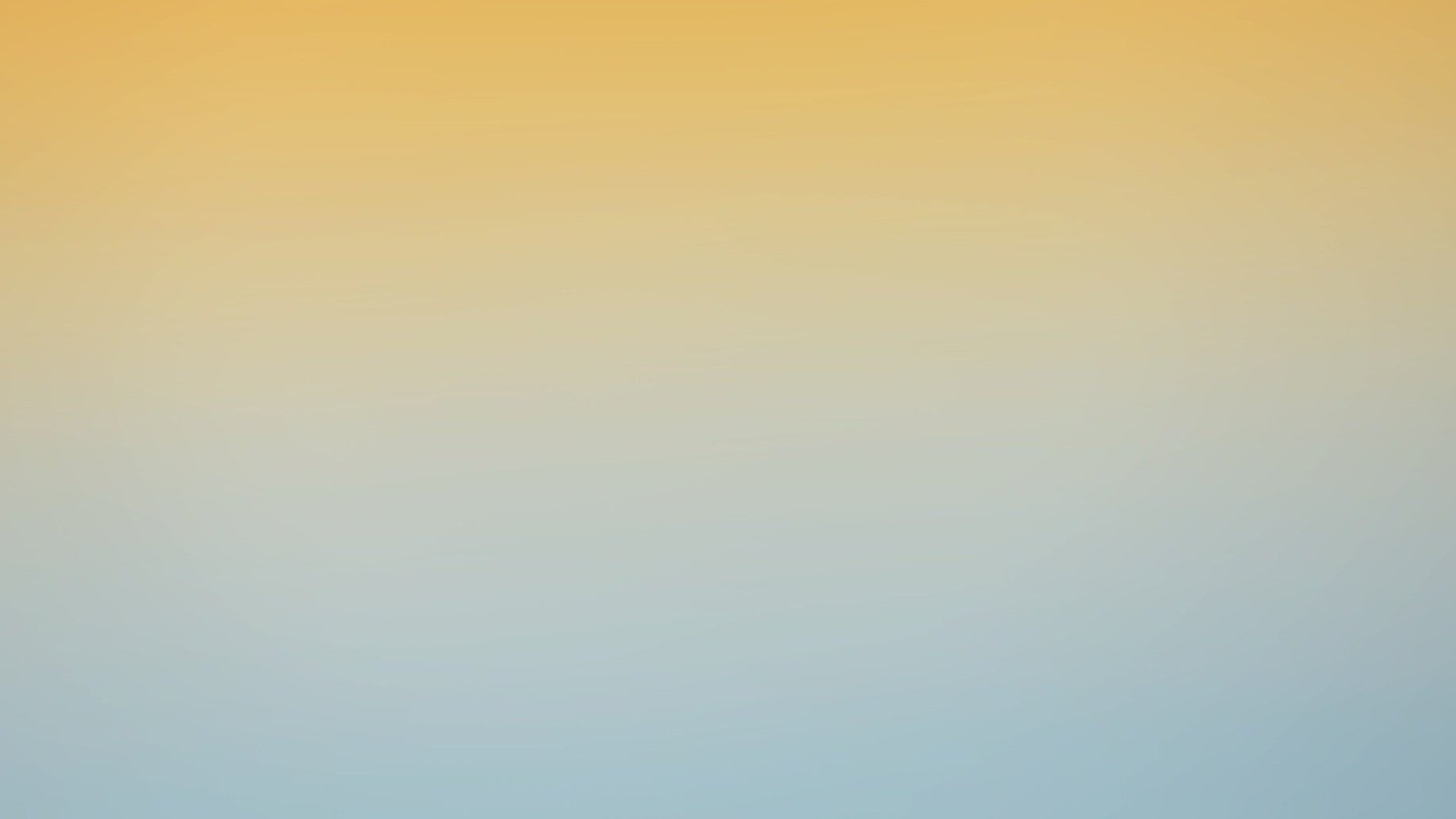
Timeline
October 2021 -February 2022 (5 months)
Team
Isabella Ferracci Matteo Orsini
Technologies
Illustrator, Photoshop, Rhinoceros, Keyshot, Figma
Material Design, Prototyping, Technologies of Innovative Materials, Bio-Materials research, Experiment
Methods
The project has been developed in the Material Studio at Sapienza University. The goal of the project was to research and understand biomaterials, then develop our own biomaterial from organic waste and eventually create a product that takes full advantage of one or more of the properties of the material.
Brushcob has received an Honorable Mention in the Cumulus Green 2022 Competition.
Brushcob is a set of three scrub brushes that takes advantage of the material abrasive properties.
All of the brushes are made following hand ergonomics in such a way as to make their use pleasant and comfortable for the user. The abrasive nature of the corn cob is used here to exfoliate the skin, and thanks to the glycerin, the skin remains soft and smooth.
The three brushes differ not only in shape and size but also in the different concentration and granulometry of the corn cob.
After each use, the product can be left to dry in the air, like a soap bar. After several uses, the brush will begin to degrade and can be safely disposed in the organic waste, thanks to the presence of biodegradable ingredients.
Cons
Presentation Video
The process
Step 1: Research
The first step was to figure out what kind of waste we wanted to work with. The first waste we selected was pistachio shell.
Pistachio Shells
Pros
✓ Pleasant texture
✓ Very hard surface
🗴 Very hard shell
🗴 Difficult to crush
🗴 Long time to crush
🗴 Difficult to find
🗴 Breaks the home blender
Corn Cob
✓ Pleasant texture
✓ Easy to crush
✓ Resistant
Pros
Cons
🗴 Absorbs lots of water
🗴 Takes time to dry
After various tests and recipes, we decided to work with the corn cob waste because, based on its characteristics, it seemed interesting to continue experimenting with it.
It is a waste material coming mainly from the food industry, where the only part that is used is the kernel which can then be processed into flour, dried, or steamed. The corn cob is produced from the ear of the corn, from which the fibrous part is extracted and dried. More specifically, the corn cob is the core of the plant, where the kernels of corn are arranged. Because of the large amount of water needed to grow corn, it is found mainly in humid regions with ample water resources.
For example, in Italy, it is more common to find large corn cultivations in the northern regions rather than in the center or in the south of the peninsula.
As a matter of fact, a part of the discarded cob is already reused in different fields and in various forms:
in the production of animal bedding;
as bio-fuel for domestic heating systems
in the mechanical industry, where it is mainly used to degrease, clean and dry metal parts:
in the gold jewelry sector, it is used to polish pieces before finishing;
to make smoking pipes;
as support in the pharmaceutical sector;
as fodder supplement or support;
in construction to restore wood surfaces, marble etc..
The second waste we wanted to investigate was corn cob.
Step 2: Experimenting
Recipe Testing
Ingredient testing
Thickness and recipe
Finalizing our recipe
Once we came up with our base recipe, we started experimenting with the ingredients in order to understand which were the most interesting properties.
Thickness Samples
Color Samples
Texture Samples
For this step, we initially considered all the samples and then went on to define a couple of ones that could actually be used to design the products. An important aspect on which we wanted to focus was the interesting relationship between water, cob and glycerine.
It was important for us to select those samples that kept their shape and had a good balance between resistance and pleasantness.
The two samples selected are:
Step 3: evaluation &proposals
Waste: mixed grain corn cob
Binder: Potato starch, water, glycerol, vinegar
Texture: mixing the moderate and raw granulometry.
Waste: finely sharded corn cob
Binder: Potato starch, water, glycerol, vinegar
Thickness: 4 mm
Recipe
Water
Potato starch
Cob (dusted grains)
Glycerol
Wine vinegar
Thickness
50,0g
13,8g
5,5g
13,6g
2g
3mm
Recipe
50,0g
13,8g
8,0g
13,6g
2g
3mm
Water
Potato starch
Cob (mixed grains)
Glycerol
Wine vinegar
Thickness
Evaluation
After many design ideas, we decided to land in the field of beauty tools. This choice was done mainly for the fact that the ingredients used to create the material were skin friendly. In this sense, we believed it would be interesting to work in the field with this material. Next, we began to experiment with shapes and functions.
Basic rectangular shape to create exfoliating pads. Shape too basic, hard to grab;
Circular shaped pads. Shape too simple, hard to grab;
Glove-shaped kind of pad that would wrap the hand and make it easy to use in the shower. This hypothesis was discarded because the material breaks easily at the thickness at which the glove would be produced.
Pads with different grain size for different exfoliation. The central sketch is a soap bar wrap. Soap wrap breaks easily and unfit for different soap shapes;
Our final proposal is a summary of all the previous tests, in which we understood how our material behaves in different contexts and in different forms.
The key aspects we decided to apply to our proposal are:
make a 3D solid product, not a flat surface;
exploit the humidity of the material when it is wet;
use the binder and other ingredients as the plus value of our product;
replicate the organic nature of the material also in the morphology;
Step 4: final proposal
We used the storyboard to better understand the possible user experience and after having users test the product, we confirmed the user path and the practicability of the brushes’ functionality
Storyboard
Benchmarking
Process diagram ( Life cycle)
Technical Drawings
Once the overall shape of our products has been settled we developed the 3D models on Rhinoceros. In order to understand if the ergonomy was correct, we did some printing tests of the products with the 3D printer. Once satisfied with the shape, we designed and printed the molds necessary to create the prototypes of the products with the materials we developed.
Step 5: prototype
The 3D-printed molds were the result of an analysis that had to take into account the extraction of the dry part. As you can see in the photo, it was divided into three parts in order to facilitate the extraction of the piece.
Once the molds were obtained, we prepared the material, poured it into the mold, and closed the mold. Once the material cooled down in the mold, until it reached room temperature, we carefully pulled it out. This operation was done very attentively because the material was sticking to the inside walls of the mold.
The cooled, but still wet/humid piece was then placed in the dryer in order to dry it out and remove as much water as possible.
Following the previous steps, we managed to make the three working prototypes of the brushes.
Face Brushcob
Fine-grained prototype
Feet Brushcob
Mixed-grained prototype
BodyBrushcob
Fine-grained prototype
Product description
After a careful analysis of the selected samples, we explored the various characteristics of the material through the various proposals. During the examination, we acknowledged that one of the most interesting properties to be investigated was the degree of abrasion of the corn, caused by the characteristics of the granulometry.
Our design proposal was born precisely considering the following material properties:
Abrasion for different scrub methods;
Skin-friendly;
Skin softening thanks to glycerin and potato starch;
Odorless in contact with water;
Rigidity for in-mold production;
The largest brush is made of fine cob grain, as one of the small ones for the face. Its use is designed to gently exfoliate the body, which is why its size is larger than the previous ones and it can be comfortably used during the shower. In this case, there are two handles, in order to have a more stable grip on the brush.
One of the small brushes is made from the cob in the form of a finer grain size and it is recommended to be used on delicate skin, like on the face. The single ergonomic handle allows users to have an intuitive and secure grip while using the brush.
The other small brush is made of bigger-sized grains: it contains medium grains (0.2mm-1mm of diameter) and large ones (1mm-2.5mm of diameter). It is designed to be used for the feet, which require more intensive exfoliation, made possible thanks to larger grains.
Conclusions
The topic of biomaterials has always been of personal interest to me, and I must say that this project reflects my interest in sustainability, and the need for circularity in product design, production, use, and disposal of products.
One aspect that I found extremely exciting was to first start the design process not from the product itself, but from the material. This different approach can be a way to design products more consciously, really understanding the impact that the products we design will have not only on the environment but also in terms of the time and amount of labor required in production.
Also, having the possibility to experiment firsthand with the material has been a good practice to develop a precise working method that allowed countless recipe trials following a precise logical pattern, until arriving at the final appropriate one.
Things I would have done differently:
experiment more with the material and with the dosage of some ingredients;
collaborate with activities that have big amounts of organic waste and use that as the base waste for our material;